Filling and closing module
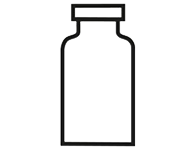
Machine type KSF 5105
Machine module KSF 5105 fills and closes bottles and vials in the VarioSys production system. The dosing station with ADVANCEDfill technology is designed to process liquid products using rotary piston pumps. However, it can also be equipped with alternative dosing technology such as peristaltic pumps or a time-pressure dosing system. Powder products can also be processed with our add-on powder dosing module. After the dosing cycle, the containers are closed fully automatically with up to two different types of closure. Insertable closures and plain crimp caps, as well as pre-assembled caps such as flip-off caps, flip top caps, flip tear up caps etc., are processed reliably and gently. In accordance with the overall machine concept, this module is designed to feed closures to the pick-up position with absolutely minimal particle emission.
Please find further information about our innovative and highly versatile VarioSys production system here:
www.variosys.com
Please find further information about our innovative and highly versatile VarioSys production system here:
www.variosys.com
HIGHLIGHTS
- Mobile, space-saving production system in an isolator
- Liquid or powder products
- Up to two different types of closure
- Scales for 1-100 % in-process control
Type of machine | Output | Processing range |
---|---|---|
KSF5105 |
|
|
Pharmaceutical design
Easy and centralized operation
Compact design
Low-particle closure feed
- Alternative dosing systems
- 100 % In-Process Control (IPC)
- Gas flushing after filling and during closing
- Bin and feed unit for optimized closure supply
- A range of checking and alarm devices and counters
- Software upgrades
- Qualification (IQ/OQ)
ADVANCEDfill ensures that optimal use is made of your product batch.
ADVANCEDfill is a highly effective solution for processing your product. All containers in a batch are filled to the optimal level so that, at most, only the last container may need to be rejected. The ADVANCEDfill dosing system is equipped with a freely positionable needle holder. Product is dispensed directly into containers on the scales during start-up and running empty. This allows dose quantity to be monitored and setpoint deviations to be corrected in situ.
Benefits of the ADVANCEDfill dosing system:
- No need for manual intervention in the dosing area, e.g. during start-up or running empty
- Optimal product utilization
- Availability from batch sizes as small as 1
- Resource-friendly technology
G-Con PODs® Unique cleanroom infrastructures
The standard POD cleanroom unit is comprised of classified space (shown center), personnel and material airlocks (left) and a mechanical space (right). The mechanical space typically contains an air handling unit, the fire suppression system, and control/access points for utilities. Ductwork from the air handler to the clean space, integrated process piping, and fire suppression piping is contained inside the POD ceiling plenum for efficiency and compactness.Dosing systems
Rotary piston pumpsThe rotary piston pumps comprise only two parts. The dose is defined by the pump stroke setting. They are self-priming and dispense pharmaceutical products very gently and with great precision.
Single-hose peristaltic pumps
Only one product hose is required from the product vessel to the dosing needle. The single-hose peristaltic pumps do not require a Y-manifold, which means that the dosing system itself is very straightforward and easy to use.
Time/pressure dosing system
Product is supplied from a dosing vessel equipped with a precision pressure controller. Only one product hose is required from the pressure controller to the dosing needle. This electronically controlled dosing process allows production data to be acquired and documented.
smartline
Are you looking for an approved off the shelf machine concept with short delivery times, but still want to be able to optimize your line to suit your specific needs?By choosing our smartline concept you can select your personal solution from pre-engineered options and still maintain your flexibility. smartline guarantees a more efficient project workflow. Maintenance, qualification and spare parts procurement are not only faster, but also easier to handle over the entire life cycle of the line. Eliminate time-consuming engineering phases and benefit from reliable solutions that come ready to use straight out of the box.
Zero Reject
The Zero Reject Principle is a concept centered around technical features with a clearly defined goal: maximizing efficiency for our customers. The aim is to avoid product loss, be it due to overfilling or underfilling, missing closures or difficulties with the supply of product supply to the individual dosing positions. To mitigate these and other potential factors that could negatively impact efficiency and output, we offer the following solutions as part of our standard portfolio:- 100 % IPC bei voller Leistung
- Re-stoppering
- Refilling on the weighing cell
- Re-capping
- Crimp-Cap-Inspektion